A “proportional” isolation valve can bring the next level of control and design for engineers, especially in life science industries.
Doug Paynter, Clippard
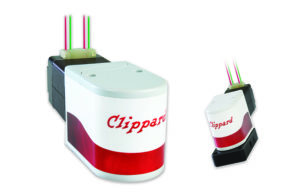
The Eclipse proportional isolation valve [Image courtesy of Clippard]
When we talk about proportional valves, whether they are pneumatic or hydraulic, we typically refer to valves that vary their flow path when you apply an increasing or decreasing amount of power/current to the proportional valve’s coil. This input to the coil will generate an ever-increasing (or decreasing) magnetic field capable of moving the proportional valve’s internal poppet or spool-designed mechanism. For example, using a low wattage pneumatic proportional valve, 0-185 mA (nominal 0-10 VDC) can be used to generate 0-65 LPM @ 100 psi working pressure. Another means of proportional control would be using a stepper motor to position a needle or plate.
So, typical proportional valve performance provides smooth, repeatable control of all types of inert gases and media — or at least that’s true if we do not use the word “Isolation” in the valve’s description.
There are all types of isolation valves in the field today — pinch, rocker and diaphragm valves, to name a few types — where their job is to ensure that whatever media is processed through the wetted area does not encounter any other materials that can contaminate that media.
Here are four contributing factors that all need to be first and foremost when designing an isolation valve:
- Dead volume. The volume inside the valve cannot be flushed during normal operation. Minimizing or eliminating dead volume is essential in applications where cross-contamination is an issue, such as drawing diagnostic samples from multiple patients.
- Internal volume. The volume trapped inside the valve assembly when the valve is closed.
- Swept volume. The volume of the flow path within the valve assembly. A streamlined flow path where swept volume is equal to internal volume means zero dead volume.
- Wetted materials. Any material that comes in contact with the media flowing through the valve.
Taking in all the factors as mentioned earlier, we have with isolation valves and now putting them towards a “proportional” isolation valve brings a next level of control and design for engineers to consider, especially during the medical/life science industry evolution we’re going through now. Providing the ability to vary the isolated wetted areas flow path is paramount to sensitive application success.
Whatever the means of isolation, eliminating the pulse, shock, on/off characteristics of a standard Isolation valve is achieved with a proportional isolation valve. It’s now possible to achieve soft start/smooth delivery of sensitive media to the test area. Proportional isolation valves can also provide enhanced close-loop results — compensating for various viscosities, repeatable flowrates, positive and/or negative pressure variation, Bi-Directional control, Latching capabilities at specific flow rates and more.
Doug Paynter is proportional valve & controls product manager for Clippard in Cincinnati. He has over 30 years of application experience within the industrial fluid power, medical and life science industries.
The opinions expressed in this blog post are the author’s only and do not necessarily reflect those of MedicalDesignandOutsourcing.com or its employees.