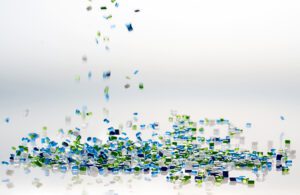
A mixture of various enhanced and transparent specialties resins [Image courtesy of INEOS Styrolution]
Styrenics is a common material used in a diversity of medical applications across the entire healthcare industry, and there are many good reasons why.
Alexander Silvestre, INEOS Styrolution
Styrenics and plastics in general have a well-established position as key raw materials within the healthcare industry. Now, more than ever, in the face of evolving technology and human health, supply-chain reliability, and a clearer focus on sustainability, design engineers are finding value in styrenics as foundational building blocks for undertaking projects to refine existing applications and/or in the development of next-generation medical devices.
1. Versatility of styrenics
Styrenic materials are ideal for an abundance of diverse medical applications thanks to their physical attributes, ease of processing in a manufacturing setting, and ability to comply with many regulatory guidelines. For example, acrylonitrile butadiene styrene (ABS) is a dominant resin in common medical devices such as inhalers, injection pens and portable insulin-delivery devices. Since these items are frequently carried outside the home or hospital, they need to be aesthetically pleasing, lightweight and demonstrate excellent chemical resistance, all while meeting a variety of physical properties. ABS is a fantastic fit.
Other examples include polystyrene, often used in labware and home-testing kits. Styrene butadiene copolymer (SBC), styrene acrylonitrile resin (SAN) and other transparent styrenic products can be found in applications ranging from medical packaging, IV components and a variety of fluid containers and syringe bodies.
Medical design engineers need to consider the patient end-use, understand the possible interaction with medicinal drugs, and ensure materials are fully vetted for safe use when potential for contact with drugs or bodily fluids exists. Whether for transparent fluid containers, drip chambers in IV sets, or medical packaging, styrenic materials meet a complex range of requirements and continue to be a material of choice by designers.
2. Supply-chain integrity
When it comes to material selection for medical devices, in addition to technical and regulatory specifications, original equipment manufacturers (OEMs) are now finding it necessary to assess supply-chain reliability. Medical design engineers have expanded their evaluation on materials and not necessarily limited themselves to the one or two products they have historically chosen.
In addition to the technical and regulatory concerns, material selection will also include whether a material is available from more than one facility, in multiple regions, and whether it is still a cost-effective solution for patient care. The reliable availability of styrenic materials ensures efficiency in the intricate manufacturing process of medical devices.
3. Styrenics and sustainability
Raw material suppliers are increasingly focused on reducing product carbon footprint (PCF) for themselves and their customers. As the leading global styrenics supplier, INEOS Styrolution has made a strong commitment to supporting sustainability objectives and a plastics circular economy. Efforts are underway to implement new programs such as use of bio-attributable feedstocks, developing chemical recycling technologies where PCR materials can be converted back to virgin styrene monomer, and implementation of mechanical recycling programs.
Our parent company, INEOS, has set a global corporate objective to be carbon neutral by 2050 and has engaged with a number of the largest medical OEMs to see how these programs can help drive their own downstream sustainability projects.
Looking to the future
Medical-design engineers are bound by a profound matrix of requirements within the medical spectrum, notably the traceability and regulatory needs of critical patient-care applications. With their immense versatility, established prevalence within healthcare applications and sustainability potential, styrenic materials are helping to innovate the next generation of medical devices into the future.
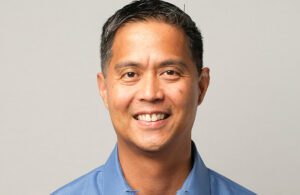
Alexander Silvestre [Photo courtesy of INEOS Styrolution]
Alexander Silvestre is the global director of healthcare at INEOS Styrolution. He is responsible for setting strategic and commercial direction and develops and maintains the company’s global policy to establish guidelines related to their products for pharmaceutical applications and use in medical devices.
How to join the MDO Contributors Network
The opinions expressed in this blog post are the author’s only and do not necessarily reflect those of Medical Design & Outsourcing or its employees.