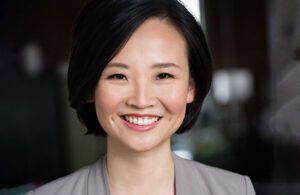
CL Tian is co-founder and CEO of Phiex. [Photo courtesy of Phiex]
MedTech Innovator winner Phiex is working with medical device manufacturers on an alternative to ethylene oxide (EtO) sterilization.
The new method uses dry chlorine dioxide gas generated inside the medical device’s product packaging. The powder turns into a microbe-destroying gas when exposed to light, Phiex co-founder and CEO CL Tian said in an interview.
Medical device manufacturers can either integrate the powder into their product packaging or as a secondary pouch. And so far, most devices that can be sterilized with EtO can be sterilized with the Phiex process, Tian said.
EtO is the leading sterilization method for medical devices. Manufacturers and contract sterilization firms use EtO on more than 20 billion medical devices every year, or approximately half of all devices that require sterilization.
But the medtech industry and FDA are exploring alternatives to EtO due to safety concerns about sterilization facility emissions. And industry association AdvaMed has warned that EtO sterilization capacity is already maxed out.
Chlorine dioxide as an alternative sterilization method

Phiex’s medical device packaging sterilizes medical devices by releasing a dry chlorine dioxide gas when exposed to ambient, broad-spectrum light. The gas seeks the bound water in the cell wall of bacteria and essentially oxidizes the cell membrane. [Illustration courtesy of Phiex]
Chlorine dioxide gas has been EPA-registered as a sterilant since 1988. It’s already used to sterilize medical devices in airtight chambers and is also used for food and water sterilization. The gas has not been linked to cancer or birth defects, though the FDA has had to warn consumers not to drink liquid chlorine dioxide products dangerously promoted as medical treatments.
Tian characterizes Phiex’s in-packaging sterilization as a gentle process, with no need for humidity, temperature or pressure pre-conditioning. Generating chlorine dioxide gas from a solid-state powder allows Phiex to control the concentration of gas needed to sterilize a particular device inside its packaging.
“We have a proprietary, dry state powder that we mix directly into the packaging,” she said. “When it is exposed to ambient light, there’s a reaction and we generate what we call a micro-atmosphere of chlorine dioxide gas. … It has excellent material compatibility, and that’s been a major concern for the OEMs with any alternate sterilization modality.”
The Phiex approach can also be used as an alternative to radiation or heat sterilization methods, which can discolor or damage medical device materials such as silicone, polyurethanes, polyethylene, polyolefins and other sensitive polymers.
“We haven’t seen a material impact in our studies with our customers. There’s no change in mechanical properties, molecular weight, tensile strengths or coloration,” Tian said. “And that’s even with us exposing it to much higher concentrations of our dry — dry being the operative word — chlorine dioxide than we would expect in an actual commercial setting.”
Another advantage over radiation sterilization is that Phiex’s sterilization process doesn’t damage electronics. That’s helpful for device developers who are integrating batteries and electronics for the first time into a device that could previously be sterilized with gamma rays, for example.
Radiation may remain the method of choice for manufacturers that need to sterilize inside airtight compartments where EtO, chlorine dioxide and other gases can’t reach. And while radiation and EtO sterilization need sterilization chambers and large facilities with expensive equipment like particle accelerators, those methods may still make sense for bulk sterilization of pallets of hardy devices.
“Where we play well is at the device level, sterilizing one or a couple inline,” Tian said. … “It’s a completely different way of thinking about how we sterilize.”
How Phiex works with manufacturers
Phiex is currently developing custom-developed packaging material to manufacturers for their production lines, but Tian declined to name customers.
“The business case for moving to a modality like ours — inline packaging-based sterilization modality — is so attractive from a strategic advantage perspective that even if we wanted to, our customers have been quite purposely hush-hush about working with us,” she said.
Tian explained how Phiex works with customers using hypothetical Class II, Class II and FDA-cleared 510(k) devices.
“You assemble it in your manufacturing line, put it together and place it into your primary packaging, which usually has a layer that is gas permeable if it’s currently sterilized with ethylene oxide,” Tian said. “Let’s just say that customer wants to use a secondary packaging, meaning after they place it in their primary and seal it, they can place some number into the secondary pouch, seal that, and start to sterilize it. After the cycle time is up, they can open it, place it into their paperboard carton, into their boxes, and then assuming they release the batch according to their release protocol, that box is now ready to go off to their point of distribution or their end customer.”
That process, Tian said, is weeks faster than sterilizing through third-party vendors, where it might take days or weeks just to make enough products to efficiently ship to a contract sterilizing facility. Depending on how backed up the contract sterilizer is, there could be more delays until the products are sterilized and returned to the device manufacturing plant or sent to a distribution center.
“Most OEM folks talk about the amount of time wasted with complications and issues that occur with sterilization, both from producing commercial products and also from taking novel products from the bench through the R&D process,” Tian said. “There’s a lot of interest in having a more sustainable and better-for-business sterilization modality.”
What’s next for Phiex?
Phiex customers are in various stages of adoption, ranging from submitting updated filings with the FDA to implementing the technology into their manufacturing lines. The first products sterilized with Phiex packaging could reach end-users in late 2023 or early 2024.
Things are moving fast for the Boston-based startup. Phiex had what Tian would only say was a “very positive interaction with the FDA” last year. Then the company won the $350,000 grand prize from the 2022 MedTech Innovator program, which Tian said was “hands down the best thing we’ve ever done.”
“There’s a lot of programs out there,” she said of the global medtech accelerator. “What makes this unique is the people in the program. They’re some of the top leaders in medtech, they’re so giving and willing to work with each of the portfolio companies — not just us — making introductions, working on the business, sharing best practices in a really open, generous way. One thing that we have in scarcity as startups is time, so any way to learn from what’s worked before, learn from successes rather than our own experience, is so invaluable. And I’ve really appreciated that community that [CEO Paul Grand] and the team have cultivated.”
What does the future hold for Phiex?
“If you had asked me where I thought we would be this time last year, I couldn’t have imagined that we’ve gotten this far and this much unsolicited industry interest and engagement with the major OEMs and major contract manufacturers,” she said. “I try to stay out of the business of predicting, because I have a suspicion that we’re going to go at a much faster clip than we’re conservatively planning.”